Damp storeroom with musty smell: specialist leak inspection
Basements and storerooms are prone to moisture problems due to multiple combined factors ranging from water pipe leaks, compromised drainage, building design problems, constructions deficiencies, building leaks, poor ventilation through to seasonal weather changes and unpredictable storms posing a high risk of groundwater seepage, high humidity, condensation, and mould.
Due to the design, basements and storerooms are typically concealed, windowless spaces constructed below ground level both in older and newer commercial buildings. The conditions translate into limited natural airflow, light, stagnant air, and higher than normal humidity levels.
High moisture is simply bad news for the building structure, the occupants and the stored contents especially in damp climates. High relative humidity often triggers a multi-dimension chain reaction: from unpleasant musty odours, spoiling stored goods, damage to building materials through to mould growth and the associated respiratory allergies and skin conditions. High levels of carbon dioxide or COâ‚‚ are indicative of poor ventilation and may cause headaches and fatigue.
Typical signs of high moisture in storerooms and basements
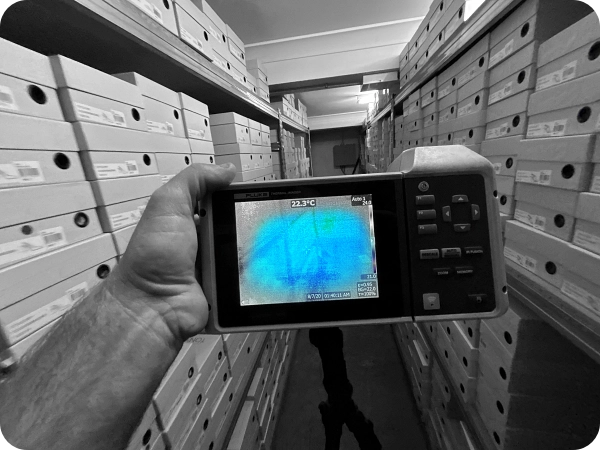
Smell
Unpleasant damp musty odours largely driven by stagnant air and exacerbated by high temperatures and densely packed areas.
Most common causes of damp and humid storerooms
Active leak
Common drivers of high humidity include ongoing water ingress inside a storeroom or basement from a leaking water pipe, blocked drains, a building leak, seepage, leaking penetration, cracks and voids, lack of maintenance.
No ventilation
Small, concealed, underground, and windowless basement and storeroom designs significantly undermine air exchange and natural airflow. This in turns lead to stagnant, damp and musty air.
High humidity
The underground design combined with the materials used often lead to high relative humidity and mould in basements. Bricks and mortar absorb and retain moisture specially without waterproofing.
Storeroom expert inspections: leak detection plus moisture and humidity
The team at Sydney Leak Detection conducts expert storeroom and basement assessments to diagnose the combined factors driving the elevated moisture, high relative humidity, mould, and dampness. With years of experience, specialist leak detection equipment, and other high-end measuring devices, the team delivers a clear and comprehensive assessment of the core issues, as well as practical, targeted, and cost effective solutions.
The construction materials used, age of the building, plus Council development restrictions, heavily restrict air-vent installation along external walls and/or sub-floor for additional airflow. Generally, building alterations and improvements may be a demanding, challenging, and costly strategy. Therefore, the installation and operation of a combination of mechanical ventilation, dehumidification and air filtration devices plus minor building improvements may be a more suitable preliminary solution to maintaining storeroom humidity levels and air quality in basements.
1 Mechanical ventilation
Ventilation and dehumidification systems aim to remove stale, humid, and contaminated air while bringing in fresh air to the basement to reducing COâ‚‚ and preventing damp air stagnation. To ensure proper air exchange and humidity control, the installation of mechanical ventilation with heat recovery may be a suitable option ,such as a wall-mounted unit.
2 Dehumidifiers
The setup of low energy dehumidifiers with HEPA filtration aims to target humidity between 40–50% RH instead of the typically higher levels recorded in Sydney storerooms and basements. Regular monitoring of humidity levels is essential, particularly following seasonal changes and/or storm events to ensure dehumidifier settings are adjusted either manually or via the built-in sensors. Many products are susceptible to mould growth, thus requiring stable humidity conditions.
3 Air purifiers
On the other hand, air purification systems filter and remove airborne particles targeting allergens, mould spores, and damp musty odours in basements and storerooms. The strategic placement of the equipment is essential to ensure effective operation either away from direct airflow or near ventilation intake.
4 Building repairs
In terms of simpler building improvements, two areas frequently overlooked include the professional application of waterproofing and insulation. Nowadays there are many innovative and effective moisture barrier solutions and specialist coating systems available for a wide range of custom settings. Some examples include negative waterproofing solutions, foam and concrete injection, protective coatings to significantly reduce vapour and moisture transfer, seepage, rising damp, active leaks and more.
5 Plumbing
Regular plumbing maintenance is a must, including the water pipework, stormwater drains, and the sanitary sewer to ensure no discharge of liquids inside the basement and storerooms. Undetected and unattended active water leaks will drive incremental water ingress, moisture, and higher humidity which are hugely problematic in concealed spaces with limited to no ventilation.
For a free discussion call our team today.